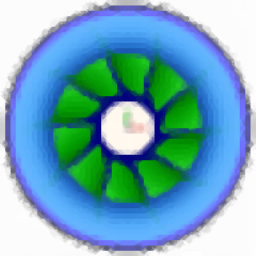
Concepts NREC CAE/CAM 2015
附安装教程- 软件大小:230 MB
- 更新日期:2019-05-13 10:52
- 软件语言:简体中文
- 软件类别:3D/CAD软件
- 软件授权:免费版
- 软件官网:待审核
- 适用平台:WinXP, Win7, Win8, Win10, WinAll
- 软件厂商:

软件介绍 人气软件 下载地址
Concepts NREC CAE/CAM是一个集设计、分析、加工于一体的研发平台,其中MAX-PAC程序是主程序的一个插件,可以访问MAX套件的CAM软件, MAX-PAC的开发旨在满足涡轮机械专用计算机辅助制造(CAM)软件的需求,并提供以下程序:MAX-5适用于特殊类型的涡轮机械部件,这些部件采用规则表面设计,先进的功能包括专利(美国专利5,391,024)侧面铣削底切减少,支持非刻划刀刃的点铣;MAX-AB能够为非规格(也称为任意或雕刻)表面涡轮机械部件生成加工指令, MAX-AB强调平滑加工指令,与高速铣削应用兼容,通常应用于使用任意表面设计的部件类别,但也可用于规则表面部件的高速铣削工艺;MAX-SB为铣削单个刀片创建刀具路径,这些部件旨在连接到较大的环上,以形成具有多个叶片的部件,通常用于轴流式涡轮机和压缩机,单个刀片通常安装在5轴机器上,使得刀片在铣削期间围绕堆叠轴线旋转。 MAX-SB包括使用角半径工具进行高效精加工的策略;MAX-SI提供铣削整体带罩涡轮机组件的刀具路径,例如膨胀机,泵,过程压缩机,涡轮机和涡轮喷嘴,MAX-SI还用于生成大型轴流压缩机,叶片和其他需要侧入加工方法的部件的加工指令。需要的用户可以下载体验
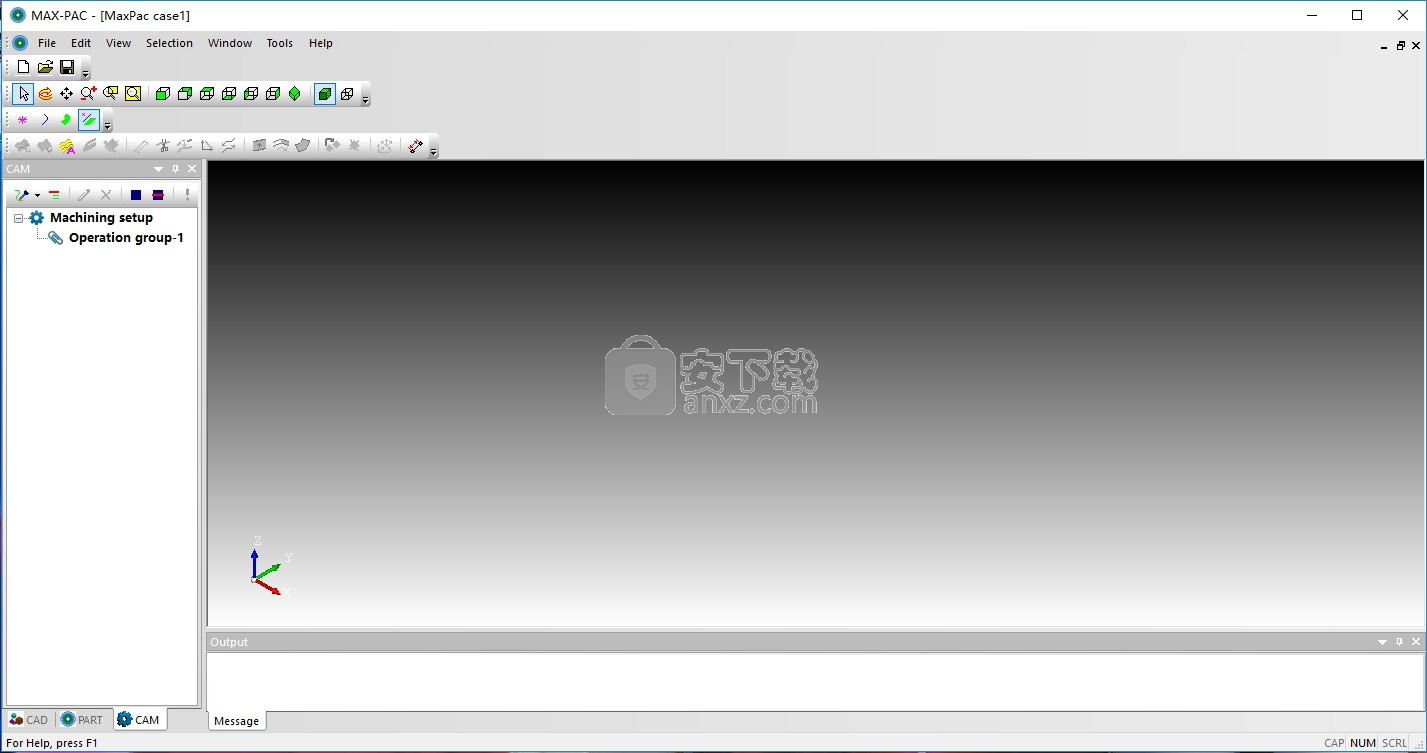
软件功能
所有MAX-PAC模块都具有以下先进技术特性:
自动构造涡轮机械功能,如边缘和圆角
用于转换常见数据格式的几何预处理器PREMAX
大大减少了编程和加工时间
刀具尺寸预测
专利(美国专利5,107,436)检测并避免刀具和刀片表面之间的碰撞,以产生平滑的加工数据。
5轴NC指令,带有可选的4.5,4和3轴输出
机器独立的APT刀具路径输出
用于5轴机床的可选定制NC后处理器
任意或雕刻的表面几何是三维表面,其定义在两个以上的数据部分。无法找到直线段来连接护罩和轮毂表面以及中间数据部分,
通常不能使用侧面铣削方法(与刀具侧面接触)加工任意表面。为了正确加工任意表面,切割器的尖端必须接触表面并在整个表面上进行。刀具方向有很多种选择;提供它不会干扰工件或固定装置,并且它处于“明智”的方向。这种加工过程称为点铣削。
加工任意表面需要大量的通道,并获得与侧面铣削相同的表面光洁度质量。即使如此,从护罩到轮毂的每次通过之间仍然保持尖瓣。虽然可以使用额外的精加工工艺来进一步改善表面光洁度,但通常希望使加工工艺形成精加工表面以保证质量和可重复性。
大多数流体动力部件采用工程设计软件而非CAD / CAM软件设计。工程软件系统使用气体速度和压力作为主要设计标准。确定几何形状以满足这些标准。
工程软件的几何结果通常表示为列表数据。 CAD / CAM软件通常描述具有NURBS表面描述的几何元素。 NURBS描述是明确的,允许不同的软件产品具有共同的产品模型。 Turbomachinery工程设计软件产品现在也使用NURBS曲面生成输出数据。
MAX-PAC支持几种输入零件几何的方法:
表格2D和3D格式
数据作为沿压力和吸力表面的点输入,或作为循环数据表示输入。数据部分应按理论流线规定,但可以通过轮毂或护罩边界轮廓进行修整,轮廓或护罩边界轮廓不需要与数据部分重合。
NURBS输入数据格式
NURBS输入数据格式允许在MAX-PAC中精确建模另一个设计或分析软件中保存的几何模型。 NURBS格式包括曲面顺序,结矢量,控制点和可选的控制点权重。
PREMAX格式转换
PREMAX将其他表格工程格式转换为可用于MAX-PAC的格式。典型的转换来自极坐标,弧线和厚度规格。
PREMAX和MAXPP是包含MAX-PAC程序安装的独立实用程序。当您在CAM窗口中选择操作并按下工具栏PP按钮时,MAX-PP程序可以调用MAX-PP的命令行版本。
边缘规格
详细的刀片设计并不总是包括边缘坐标。它有时被描述为构造规则,例如椭圆弧段。在这些情况下,必须将边构造为软件建模功能的一部分。例如,构造前沿或后沿。
一些边缘构造方法包括第一或最后一个叶片站上的内部或外部边缘,多个弧,弧和中心,或最佳拟合。椭圆形边缘形状沿叶片曲面线产生。
刀刃的形状对于部件的操作性能是至关重要的。叶片表面和边缘表面之间的混合必须是连续的并且具有平滑的曲率分布。软件中的构造方法确保满足这些标准并保持设计意图。
输入数据说明
如果输入数据符合一些基本规则,则会增强刀片几何的分析建模。
应提供足够精确的数据,以精确模拟工件。建议数据比机床数据精度和工件的轮廓公差更精确。 MAX-PAC不会提高输入数据的准确性。
沿着每个部分或从一个部分到部分的数据点的间距应该是“规则的”。样条曲线的规则间距表明相邻点对之间的距离比率不超过三比一。这有助于开发一个足够模拟所有部分的结矢量。
表示表面的数据点必须形成矩形网格(m×n)。术语矩形是指所有部分上的点数相等。
不仅应该在每个数据部分和矩形网格上有规则的点间距,而且复合节点网络还应该在两个参数方向上保持规则的间距或相干性。特定位置的几何形状的不自然浓度可能产生不可预测的表面。
软件特色
每个MAX程序都可以为以下类型的零件几何创建NC加工指令。
MAX-5 - 带刻度的表面组件,带有可选的非刻划边缘。
MAX-AB - 规则或任意表面组件
MAX-SB - 单叶片组件,带有刻划或非刻划表面。
MAX-SI - 整体覆盖的涡轮机组件。 这些部件可以设计有规则或任意表面几何形状。
在MAX-5和MAX-AB中,刀具从护罩进入零件,通常允许最短的刀具。 在MAX-SI中,刀具使用来自引线或轨迹边缘的“侧入口”进行深腔铣削。
规则表面是通过扫描两个空间曲线之间的一系列直线段而形成的三维表面。在涡轮机械应用中,空间曲线通常位于旋转表面上,称为轮毂和护罩;线段与轮毂和护罩相交,通常不会自相交,
刻划表面组件在制造方面具有成本优势。刀具的侧面在一次连续扫描中产生精加工通道。通过这种接触获得高质量的表面光洁度。对于规则表面叶轮,通常不需要手工精加工以满足蓝图规格。使用一次成型通道还可以减少制造时间和成本,而不是点铣程序所需的多次通过。
概念NREC已经支持这些想法超过三十年,并且还为生产规则表面叶片的叶轮生成专门的设计工具。最近,先进的设计工具和基于CFD的设计产生了刀片,其中许多是任意表面,可提高部件性能并增加对点铣应用的需求。
大多数刻划的表面几何形状可以使用MAX-5建模;但是,您应该避免在离心流出机器上使用径向元件的几何形状,如下所示。这些组件不满足我们对轮廓曲面的基本定义,该曲面在轮毂和护罩轮廓之间具有直线段。另外,裁决非常长,这导致制造问题,并且几乎与轮毂平行,这导致数值问题。
机加工叶轮和转子通常需要五轴数控机床。五个自由度用于控制空间中的切割点和切割器方向。重要的是使用具有足够的轴行程和精度的机床来生产部件。
一些叶片设计,包括压缩机叶片,泵诱导器和扩散器,可以使用较少的同时运动轴来加工。
五轴铣床
五轴机床设计有多种配置。用于涡轮机械应用的大多数铣床具有三个线性轴和两个旋转轴。两个旋转轴通常彼此垂直,并且每个旋转轴平行于一个线性轴。在一些配置中,部件安装在两个旋转轴上,并且在其他配置中,部件安装在一个旋转轴上,并且切割器安装在枢转轴上。
铣床除了几何配置外还具有许多显着特征。其中一些特性包括主轴数,主轴功率,轴负载和扭矩,工件和工具更换系统,计算机控制器等。还必须考虑成本,交付和服务。所有这些项目必须与您预期的机器使用情况相匹配 - 工件尺寸,材料,批量,劳动技能和可用性。
NC后处理器将刀具位置和方向的笛卡尔描述转换为机床坐标系。这些几何变换允许通过软件支持所有机床配置。主要限制因素是可用的轴范围,尤其是头轴。如下图所示,100°的轴头范围足以满足大多数离心应用。轴流压缩机和涡轮机可以使用更少的轴头范围。
其他铣床
其他铣床包括三轴,四轴,四轴半和五轴机床,在许多情况下也可以使用。
三轴机器
当切割器方向固定在与工件旋转轴平行的角度时,可以使用三轴机器。
四轴机器
通常,当刀具定向以垂直于工件旋转轴线的角度固定时,可以使用四轴机床。
四轴半轴机器
减轴加工的变型称为4½轴加工。在该构造中,头部轴线以与工件旋转轴线平行或垂直的角度锁定。
五轴机器
作为使用减轴机床的一种选择,许多五轴机床都有命令“锁定”机床轴。当机床轴“锁定”时,机床结构变硬,这可以提高切削性能
安装步骤
1、下载并打开安装数据包,得到相应的应用程序
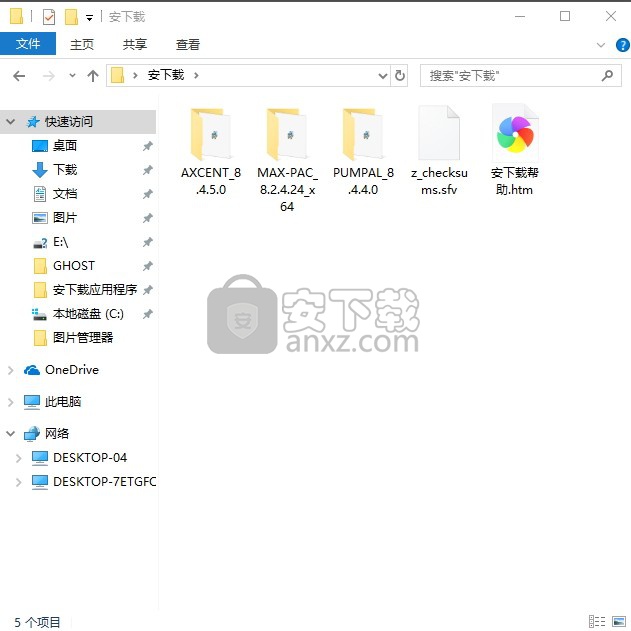
2、小编便以其中一个为用户安装解析,其他安装过程都一样
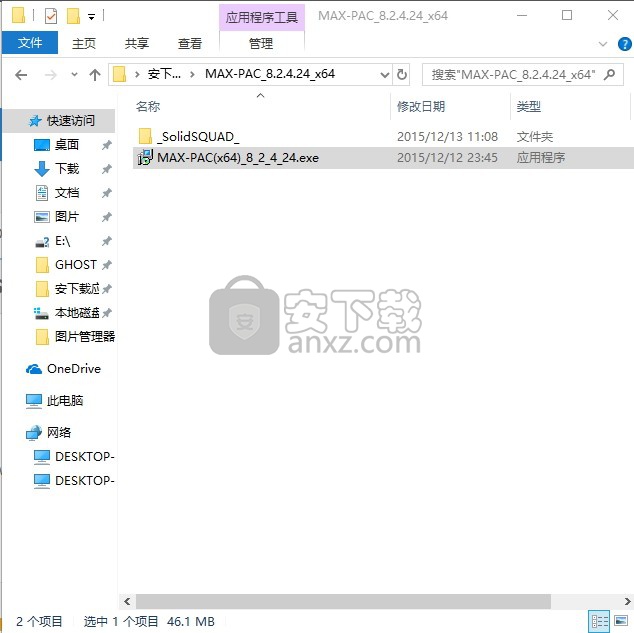
3、打开程序文件后即可进行程序安装界面
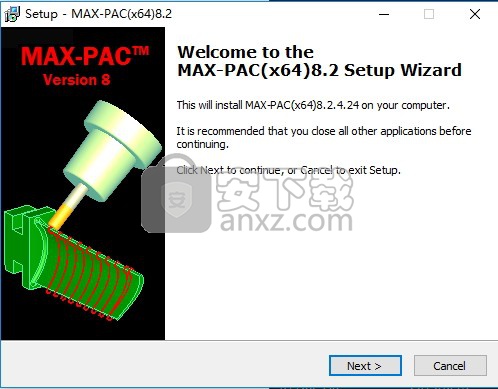
4、同意程序安装协议
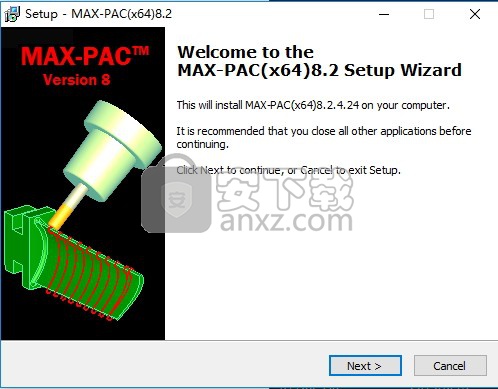
5、选择程序安装路径
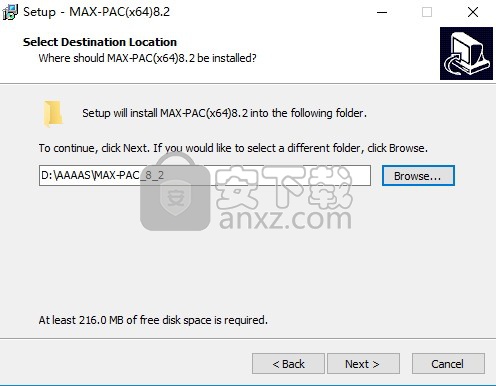
6、根据需要选择创建菜单栏
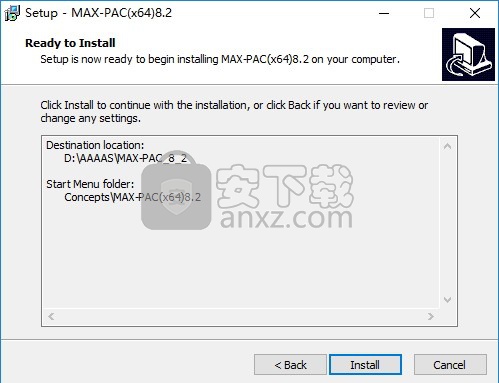
7、核对安装信息
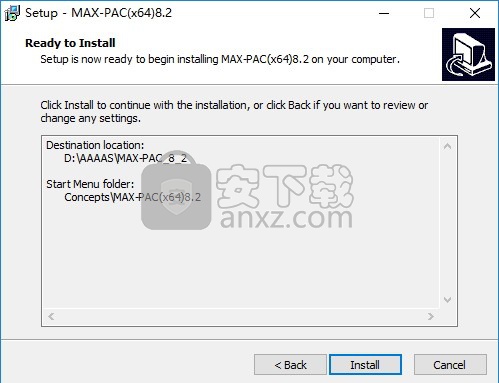
8、等待安装进度条加载完成
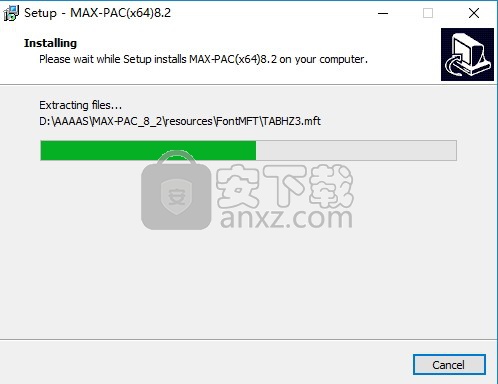
9、弹出完成界面,点击完成即可
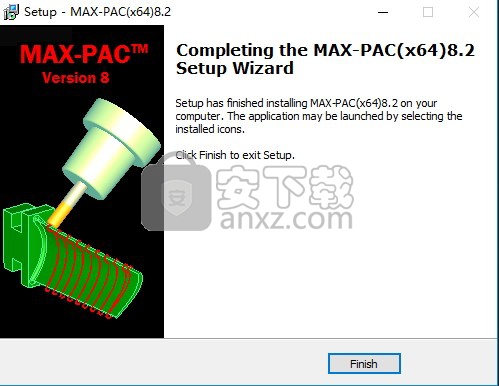
方法
1、程序安装完成后,先不要急着运行,打开安装包,找到文件
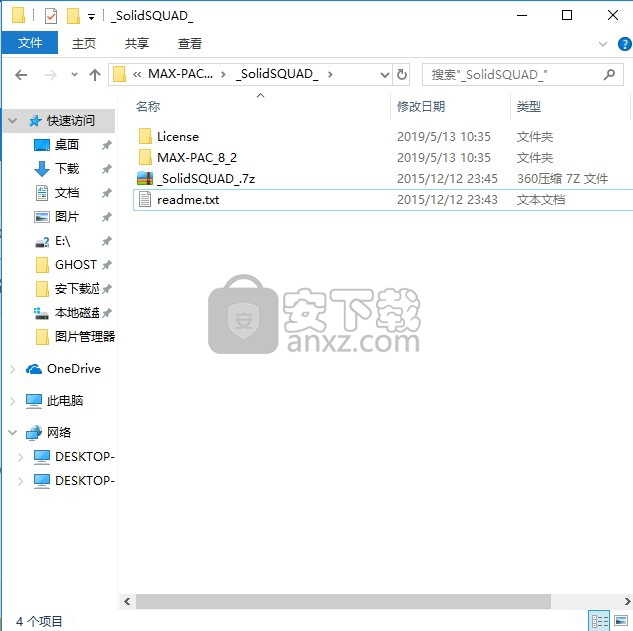
2、件文件复制到安装路径下替换程序。注意:每个程序有相对应的程序
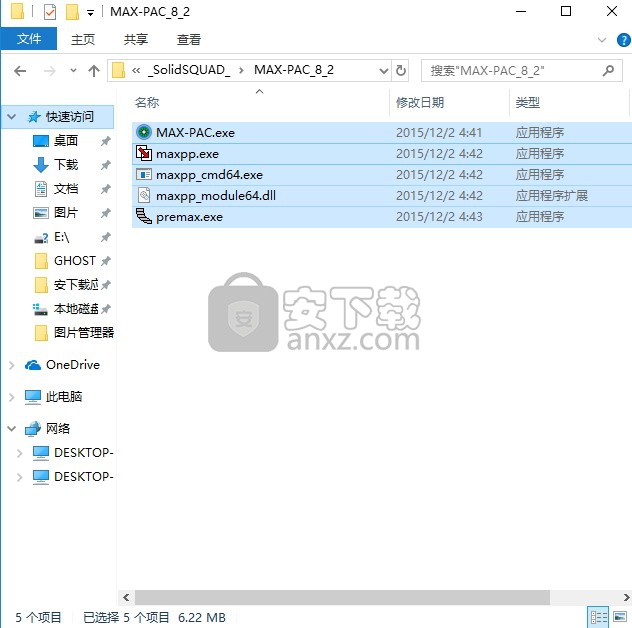
3、将文件复制到对应的安装应用程序路径文件内
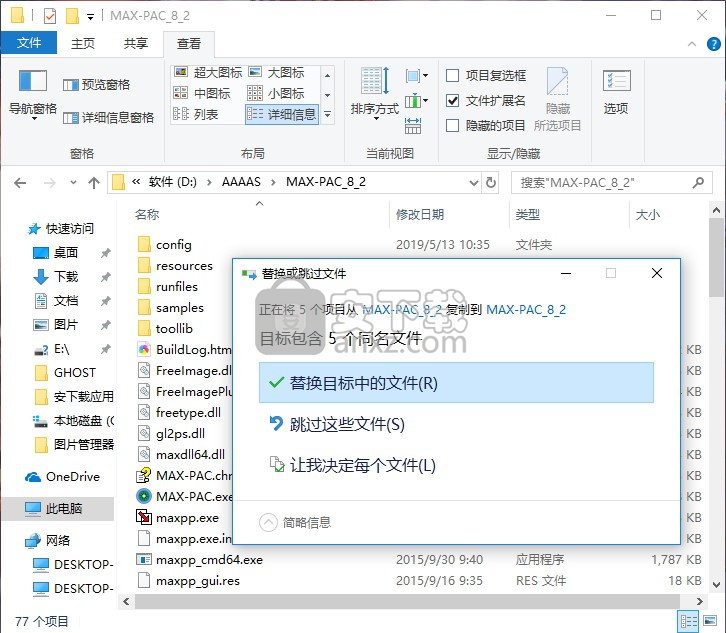
4、完成以上操作,即可将程序完成
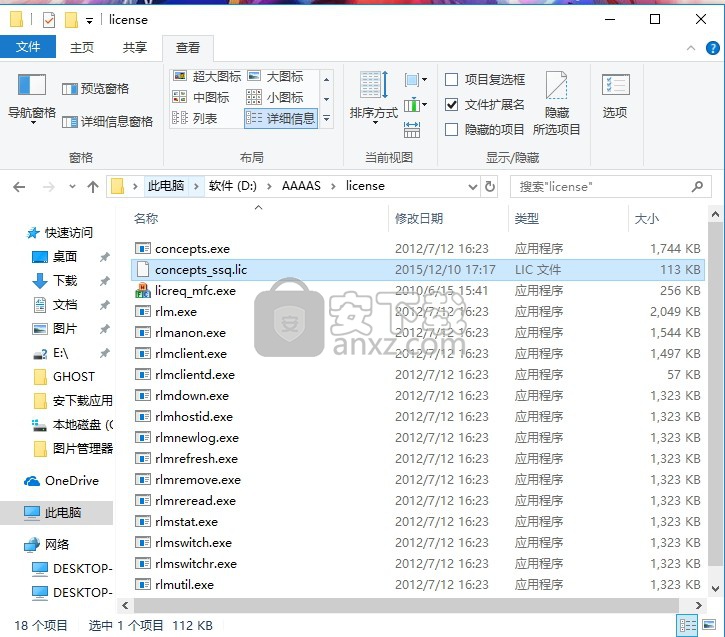
使用方法
下面列出了从输入几何文件开始运行MAX-PAC的基本步骤。
第1步:创建工作目录
在具有文件写入权限的位置创建一个空文件夹。
第2步:启动MAX-PAC
从Windows“开始”菜单中,选择所有程序 - 概念 - MAX-PAC(v.8.2)。
出现MAX-PAC窗口。
第3步:指定工作目录
从“文件”菜单中,选择“设置工作目录”。
在“Windows选择文件夹”对话框中选择目录文件夹。
第4步:复制文件示例以获取教程
将以下示例案例文件复制到您的工作文件夹中:
对于步骤6:使用IGES / STEP模型,您将需要“impeller.igs”(在...... \\ Program Files(x86)\ Concepts \ MAX-PAC \ samples中)
对于步骤7:使用数据文件,您将需要以下文件(也存储在MAX-PAC“samples”文件夹中):
impeller_mm.bnd - 边界定义
impeller_mm.edg - 边缘定义
impeller_mm.eds - 分割器边缘定义
impeller_mm.imp - 刀片定义
impeller_mm.spi - 拆分器定义
步骤5:指定单位测量
从“文件”菜单中,选择“案例单位”。
在出现的“案例单位”对话框中,选择英寸或毫米作为应用于案例的度量单位。
步骤6:使用IGES / STEP模型
注意:如果您没有CADTranslator选项,或者想要使用表格文本文件,请跳至步骤7。
要导入模型
要打开CAD文件,请从“文件”菜单中选择“导入IGES / STEP”。
在出现的“导入”对话框中,选择“插入到新图层”,然后单击“确定”。
该模型出现在MAX-PAC 3D窗口中。
查看模型
使用鼠标在3D窗口中查看模型:
要放大和缩小,请使用鼠标滚轮。
要快速缩放,请按Shift键并使用鼠标滚轮。
要旋转,请按下滚轮并移动鼠标。
要平移,请按Control键并使用鼠标滚轮。
指定刀片几何体
在PART窗口菜单树中,双击Blade。
在出现的刀片定义数据对话框中,指定刀片号中机器中使用的刀片数。
在样品叶轮中,叶片表面之一被分成A,B和L补片。
单击此刀片的B侧(CW)。
刀片的选定侧应如下所示。
在PART窗口菜单树中,单击以展开Blade节点。
右键单击Side-B,然后从快捷菜单中选择“收集曲面等曲线”。
在出现的“Face Isolines”对话框中,为节数指定2,然后单击“确定”。
对刀片的A侧重复上述步骤。
注意:如果使用带曲线的模型或创建了等曲线,则可以按照从护罩到集线器的顺序选择这些曲线,并使用“收集选定的曲线”快捷菜单选项。
指定边几何
在PART窗口菜单树中双击Edge。
在出现的“边缘定义数据”对话框中,在“类型”下拉列表中指定“外部椭圆比率[类型1]”。
右键单击该表,然后从快捷菜单中选择“添加行”。
椭圆比率列显示在表格中
在Ellipse ratio列中,指定一个值(在示例中,指定1.5)。
对于后端定义,请在“类型”下拉列表中选择“钝切”,然后单击“确定”。
要将选择级别更改为Edge,请单击“选择级别”工具栏中的。
选择定义后缘旋转曲面的曲线。
右键单击“尾随边缘”(在菜单树的“边缘”下),然后从快捷菜单中选择“收集选定的曲线”。
注意:在此示例中,MAX-PAC构造圆形边。您还可以选择“按外部点”(在“类型”下拉列表中)并从模型的圆形边缘曲面中收集iso曲线。
指定分割器几何体
双击PART窗口菜单树中的Configuration-1。
在出现的Configuration configuration对话框中,选中Configuration has SPLITTER的复选框,然后单击OK。
分割器节点出现在菜单树中(包括刀片,边缘,圆角,分离器,分离器边缘,分离器圆角和边界)。
重复上述步骤,使用主刀片CCW侧的分割器指定刀片几何图形和指定边缘几何图形。
指定护罩和轮毂轮廓
在3D模型窗口中,选择尖端(或护罩)曲面。 (见下图。)
在PART窗口菜单树中,单击Boundary以显示Shroud和Hub的节点。
右键单击“Shroud”,然后从快捷菜单中选择“从曲面收集iso曲线”。
对集线器重复上述步骤。
所选中心在3D窗口中突出显示,如下图所示。
指定圆角
双击菜单树上的“圆角”。
在出现的“刀片圆角定义”对话框中,选择“常量半径”,指定一个值(对于示例,为集线器的值为0.75。),然后单击“确定”。
构建工作模型
单击菜单树上的Configuration-1。
要构建模型,请右键单击并选择
工作模型 - 在快捷菜单上构建。
- 要么 -
单击工具栏上的。
工作模型显示为IGES模型的叠加层。
注意:要查看原始IGES模型并隐藏工作模型,请右键单击“配置-1”,然后选择“隐藏 - 所有组件”。
第7步:使用数据文件
在PART窗口菜单树中,双击Configuration-1。
在“配置配置文件”对话框中,选择“配置具有SPLITTER”。
单击“外部输入文件”部分中的“导入外部文件”。
在出现的“外部输入文件”对话框中,选择刀片(* .imp),刀片边缘(* .edg),拆分器(* .spi),分割器边缘(* .edg)和边界(* .bnd)的外部文件),然后在两个对话框中单击“确定”。
原始数据显示在3D窗口中。
双击菜单树上的“圆角”。
在出现的Blade圆角定义对话框中,选择Constant radius,为集线器指定值0.75,然后单击OK。
单击菜单树上的Configuration-1。
要构建模型,请右键单击并在快捷菜单上选择“工作模型 - 构建”。
- 要么 -
单击工具栏上的。
出现工作模型。
要隐藏数据,请右键单击Configuration-1,然后从快捷菜单中选择隐藏 - 定义点,线框U和线框V.
第8步:创建刀具路径
在CAM窗口菜单树中,右键单击“操作组1”,然后选择“新建操作 - 粗加工”。
在出现的“粗加工操作”对话框中,单击“确定”以保留所有默认值。
要构建操作,请右键单击菜单树中的粗略1操作,然后从快捷菜单中选择“生成”(或单击CAM窗口工具栏中的“生成”)。
注意:因为此示例使用自动选择工具规范(在“切割器”选项卡的“切割器规范”部分中选择)。 MAX-PAC从标准尺寸的内部列表中选择一个工具。要使用“接受自动选择的工具”选项(将工具复制到案例工具列表),必须先在“工具库”对话框中指定自动选择库。
第9步:模拟刀具路径
单击CAM窗口中的“操作”。
单击以在3D窗口中查看刀具路径;单击以隐藏刀具路径。
单击开始工具模拟。
在出现的“刀具路径模拟”对话框中,单击以开始动画模拟。
动画从3D窗口开始。使用对话框上的选项来控制模拟。
完成后,在“刀具路径模拟”对话框中单击“确定”。
步骤10:创建第二个刀具路径
在CAM窗口中,右键单击“操作组-1”,然后选择“新建操作 - 刀片完成”。
在出现的“切割器”选项卡中,取消选中“自动选择”框,然后单击“工具列表”。
将出现“工具库”对话框。
在空的工具列表表中单击鼠标右键,然后从快捷菜单中选择新建 - Ball Endmill。
在出现的“立铣刀定义”对话框中,指定以下工具参数:
球直径 - 3
切割长度 - 20
锥度-3
总长度 - 40
柄直径 - 5
要预览工具形状,请单击“更新2D轮廓/重置视图”按钮。
工具形状显示在2D预览窗口中。
在对话框中单击“确定”。
新工具将显示在“工具库”对话框的“工具”列表中。
将新创建的工具从“工具”列表拖动到“装配”列表中。
单击对话框中的“选择”按钮,然后单击“确定”。
在“操作”对话框中单击“确定”,保留“方法”,“通过”,“间隙”和“方向”选项卡上的默认设置。
要构建操作,请在CAM窗口菜单树中单击新的Blade finish 1操作,然后单击工具栏中的。
按照上面的步骤9查看刀具路径。
第11步:保存案例
要保存MAX-PAC案例文件(* .max格式),请从“文件”菜单中选择“保存”。
人气软件
-
理正勘察CAD 8.5pb2 153.65 MB
/简体中文 -
浩辰CAD 2020(GstarCAD2020) 32/64位 227.88 MB
/简体中文 -
CAXA CAD 2020 885.0 MB
/简体中文 -
天正建筑完整图库 103 MB
/简体中文 -
Bentley Acute3D Viewer 32.0 MB
/英文 -
草图大师2020中文 215.88 MB
/简体中文 -
vray for 3dmax 2018(vray渲染器 3.6) 318.19 MB
/简体中文 -
cnckad 32位/64位 2181 MB
/简体中文 -
Mastercam X9中文 1485 MB
/简体中文 -
BodyPaint 3D R18中文 6861 MB
/简体中文